STOBA R&D Results and Commercialization Plans
The Ministry of Economic Affairs Department estimated the global electric vehicle (including the BEV, PHEV, and HEV) sales volume in 2018 would grow to 7.29 million vehicles of which 85.9%, approximately 6.26 million lithium-ion electric cars, would use lithium-ion batteries as their power supply.
Safety is the primary focus of the development of vehicles that use lithium ion batteries. Lithium-ion batteries still have about a 1% risk of overheating as well as some other safety issues.
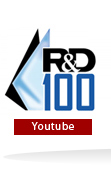
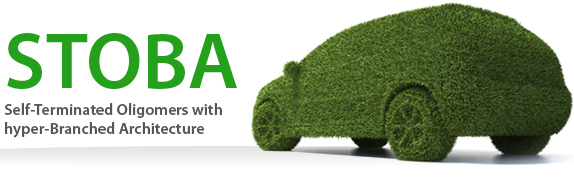
In 2008, ITRI developed a high-safety method “to terminate the high difference oligomers” (Self-Terminated Oligomers with hyper-Branched Architecture, STOBA) used in lithium battery technology. STOBA is nanoscale polymer material added to the lithium battery as a protective film adding multiple protection mechanisms. It passed the forced short-circuit puncture safety experiment, a test more stringent than those required by current international battery safety regulations. STOBA received the 2009 100 R&D Technology Awards from the US R&D Magazine and 29 patents have been applied for based on the technique.
In 2011, Amita Technologies, a collaborator in ITRI’s STOBA project, received the award of the 6th Nano Industrial Technology Elite Award for its lithium ion battery combined with STOBA technology. Dr. Jingyi Cheng, the chief executive officer of the company, said that the award winning technical characteristics of the nanoscale polymer materials in the internal lithium battery protection Mechanism (STOBA) prevent internal battery short circuit produced by thermal runaway.

Amita has been using STOBA technology by ITRI with the support of the Department of Industrial Technology Research & Development Program to create highly safe lithium batteries for electric cars with the hopes of redoubling our energy costs. Although there is a slight increase in the development potential of the electric vehicle applications, the high safety of the STOBA technology still allows for the lithium batteries to reach an energy density of 180 Wh/Kg. This production in 2012 will gradually replace the traditional lithium battery pool in order to expand more into the electric car market by actively planning to expand the plant capacity by 10-20 times, expanding even further to the domestic and export markets.